石墨散热膜
石墨散热膜是一种非常薄的GTS,综合性质的热传导材料,也称为热传导石墨膜、热传导石墨片、石墨散热片等,为电子产品的薄型发展提供了可能性。散热石墨膜具有良好的再加工性,可根据用途与PET等其他膜类材料复合或涂胶,该材料具有弹性,可裁剪冲压成任意形状,石墨散热膜厂家介绍可多次弯曲的点热源适用于将点热源转换为面热源的快速导热,具有较高的导热性能除传统方法外,散热石墨膜是提供散热管理/在有限区域内功率设备散热或提供辅助功率设备散热的理想材料。
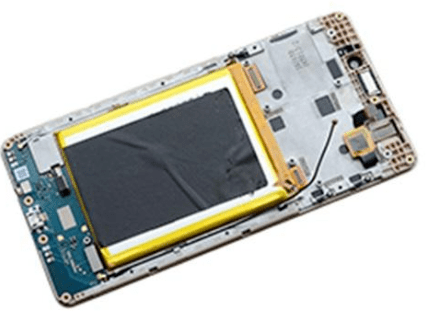
石墨膜:散热方案的主流材料
主流散热材料,单手机用量为 3~6 片石墨是相较于铜和铝等金属更好的导热材料,主要原因在于石墨具有特殊的六角平面网状结构,可以将热量均匀地分布在二维平面并有效地转移。在水平方向上,石墨的导热系数为 300~1900W/(m〃K),而铜和铝的导热系数约为 200~400 W/(m〃K)。在垂直方向上,石墨的导热系数仅为 5~20W/(m〃K)。因此,石墨具备良好的水平导热、垂直阻热效果。同时,石墨的比热容与铝相当,约为铜的2倍,这意味着吸收同样的热量后,石墨温度升高仅为铜的一半。
此外,石墨密度仅为 0.7~2.1g/cm3,原低于铜的 8.96g/cm3 和铝的 2.7g/cm3, 因此可以做到轻量化,能够平滑粘附在任何平面和弯曲的表面。基于高导热系数、高比热容和低密度等性能优势,石墨自 2009 年开始批量应用于消费电子 产品,2011 年开始大规模应用于智能手机,目前已经取代传统金属,成为消费电子领域主流的散热材料。
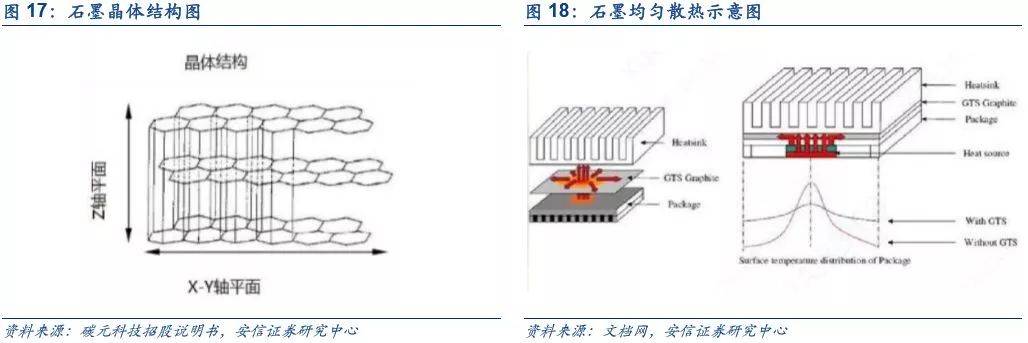
理论上,石墨膜越薄,导热系数越高。早期石墨膜厚度主要介于 20~50µm 之间,其水平轴 的导热系数介于 300~1,500W/(m〃K)。随着技术改善,石墨膜的加工工艺更加成熟,目前最 薄可到 0.01mm,其水平轴的导热效率也高达 1,900W/(m〃K)。然而,石墨散热片并不是越薄越好,关键是要将功率器件和散热器之间的缝隙填满。因此,不同应用场景下使用的石墨散热膜各有不同。
主流的散热膜有天然石墨散热膜、人工合成石墨散热膜和纳米碳散热膜三种
(1)天然石墨膜:完全由天然石墨制成,在真空条件下不会发生脱气现象,在400℃以上 的温度也可继续使用,最低能做到 0.1mm 左右,主要应用在数据中心、基站和充电站等。
(2)人工石墨散热膜:由聚酰亚胺(PI 膜)经过碳化和石墨化制成,是当前最薄的散热膜材料,最薄可做到 0.01mm,广泛应用于手机、电脑等智能终端产品。
(3)纳米碳散热膜:由纳米碳(石墨同素异构体)制成,最薄可做到 0.03mm,散热功率可 高达 1000~6000。由于纳米碳散热膜加工工序简单,只需要开模和冲切,成本低售价也低。
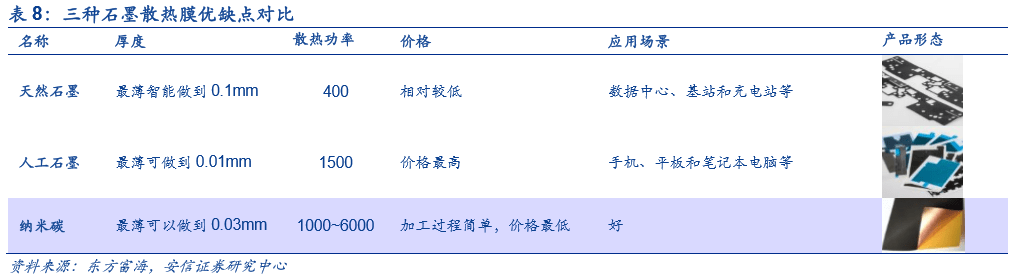
智能手机中主要使用人工合成石墨膜,用量视手机性能和要求而定,大概在 3~6 片,使用到 的部件包括镜头、CPU、OLED 显示屏、WiFi 天线、无线充和电池等。其中 CPU对散热的性能要求最高,其次是无线充,再次是镜头和电池,最后是显示屏和 WiFi 天线。目前,高导热石墨膜的价格约为 0.2~0.3 美金/片。初步估算,单机石墨膜价值量为 1~2 美金。未来, 随着智能手机更多创新型的电子化设计,单机石墨膜价值量有望进一步提升。
手机、笔电、平板以及智能穿戴等电子产品已成为我们生活中不可或缺的必需品,功能日益强大,高速处理器、高分辨率、大屏化、高像素拍摄等等,迭代更新的速度让其他科技产品望尘莫及。功能高度集成和轻薄化设计也使得电子产品的散热问题越发突出,新型高导热石墨烯散热膜开始大显身手。
石墨烯
石墨烯,英文名:Graphene,是一种由碳原子以sp2杂化轨道组成六角型、呈蜂巢晶格的二维碳纳米材料。
石墨烯导热主要通过晶格的振动,晶格(声子)通过晶体结构单元的相互谐调制约和相互的声子振动来实现对外界的热量传导。石墨烯具有高热导率的原因,主要来源于碳原子间牢固的结合力、高度有序的排列组合和微晶尺寸比较大的晶格排列。
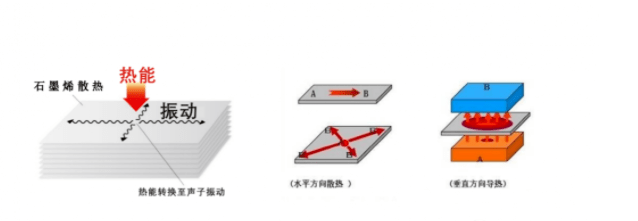
石墨烯散热膜的导热机理
石墨烯的热导率主要由石墨烯声子频率、声子自由程、声子作用过程等因素决定,不同状态下石墨烯的热导率有所差别。纯的无缺陷单层石墨烯热导率高达5300W/mK。
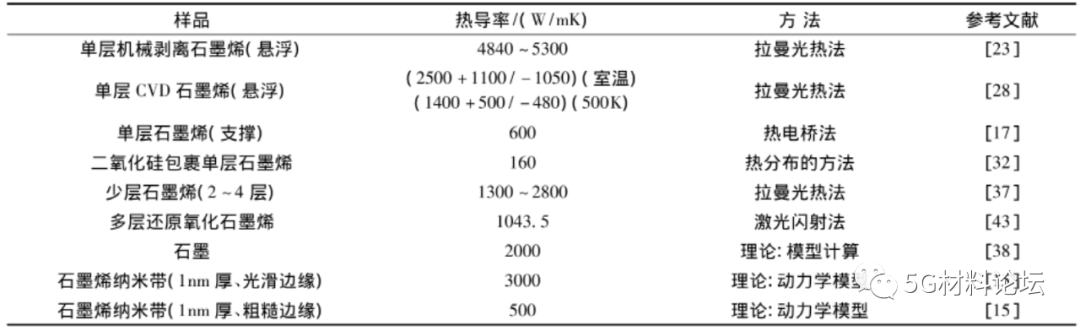
不同形态石墨烯材料的热导率
石墨烯散热膜
石墨烯散热膜是以石墨烯为原料,采用多层石墨烯堆叠而成的高定向导热膜,包含保护膜、单面胶、石墨烯膜、双面胶和离型膜等。
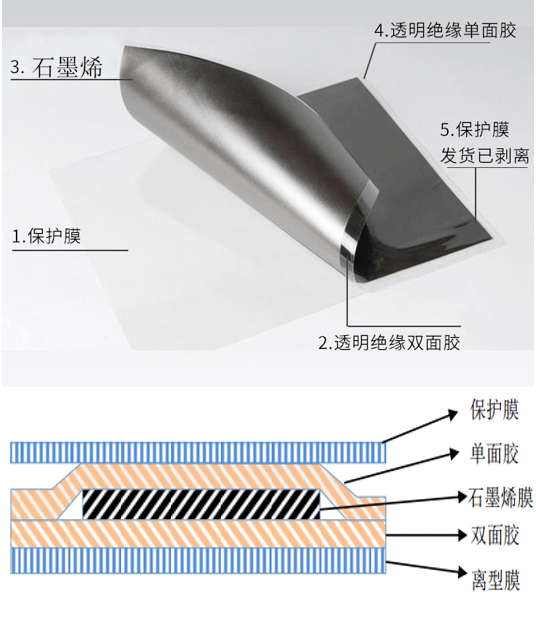
石墨烯散热膜的优点:高导热系数,可达到1200~1800W/m·K,远大于传统的金属散热材料如铜、铝;低热阻,热阻比铝低40%,比铜低20%; 重量轻,重量比铝轻 25%,比铜轻75%;散热石墨烯膜表面可以与金属、塑胶、不干胶等其它材料组合,且根据实际形状需要可对石墨导热膜进行切割裁剪。
石墨烯散热膜的生产工艺;石墨烯散热膜以天然鳞状石墨为原料制备石墨烯浆料,经过涂布、烘干后送入高温炉进行碳化、石墨化处理,后经压延、模切最终获得。
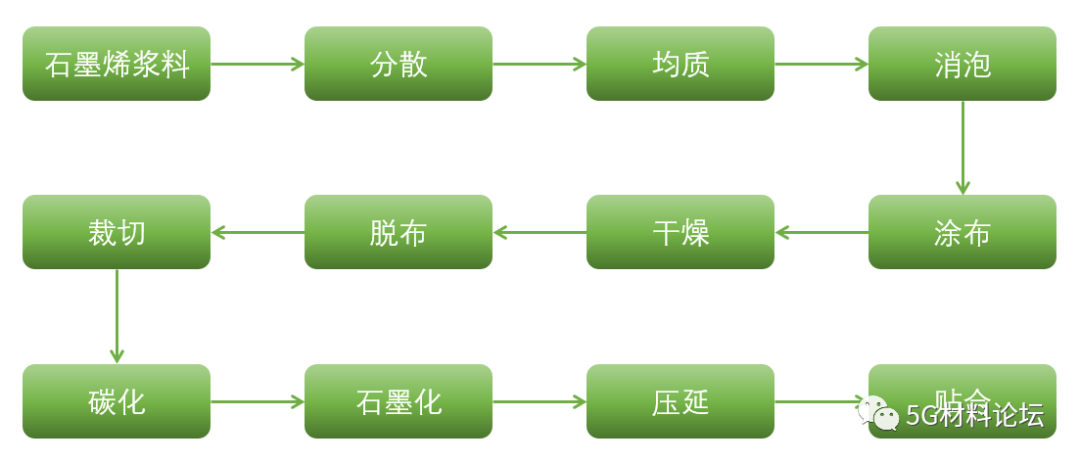
石墨烯散热膜的主要生产工艺
特别声明:本文转自互联网,如有侵权,联系管理者删除,谢谢!